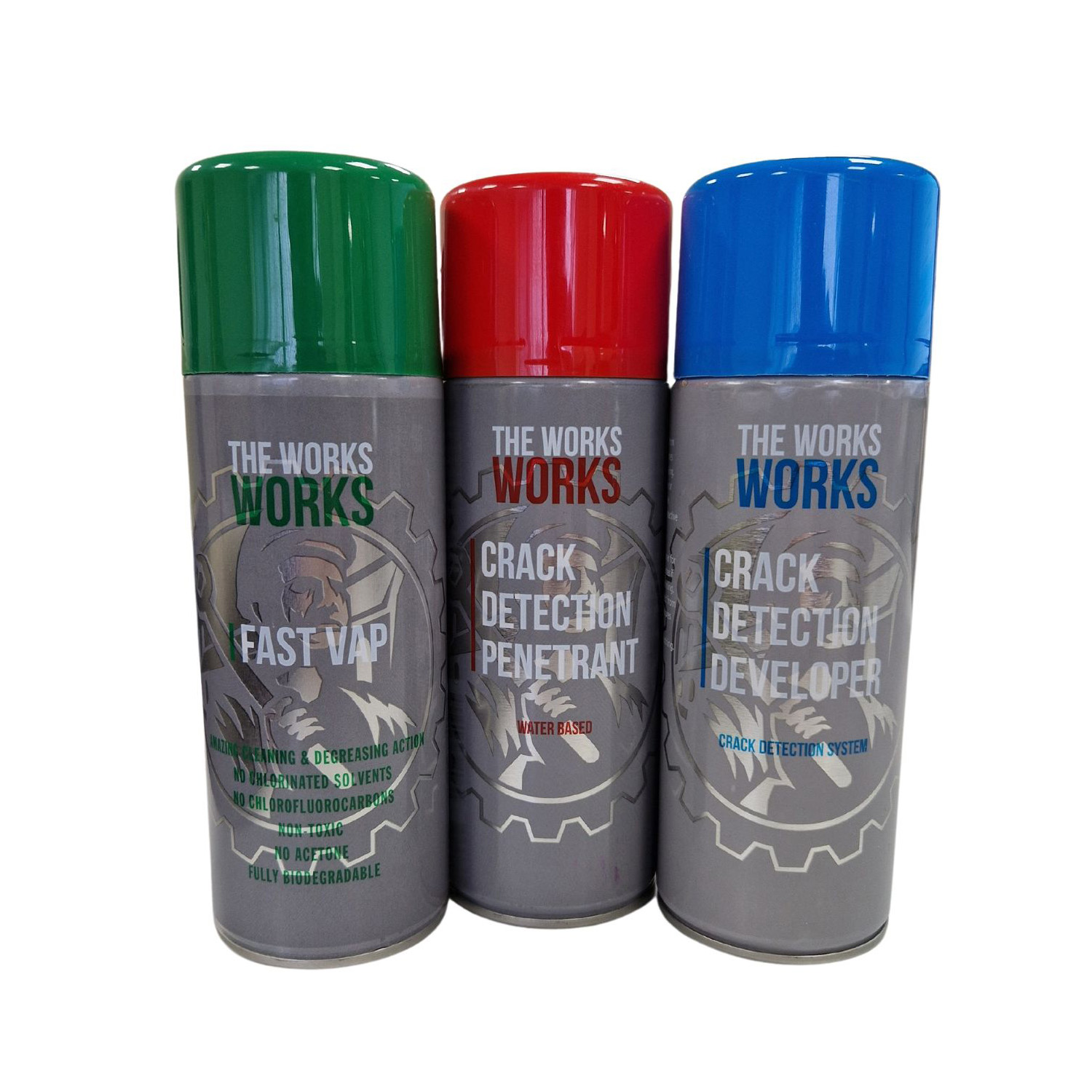
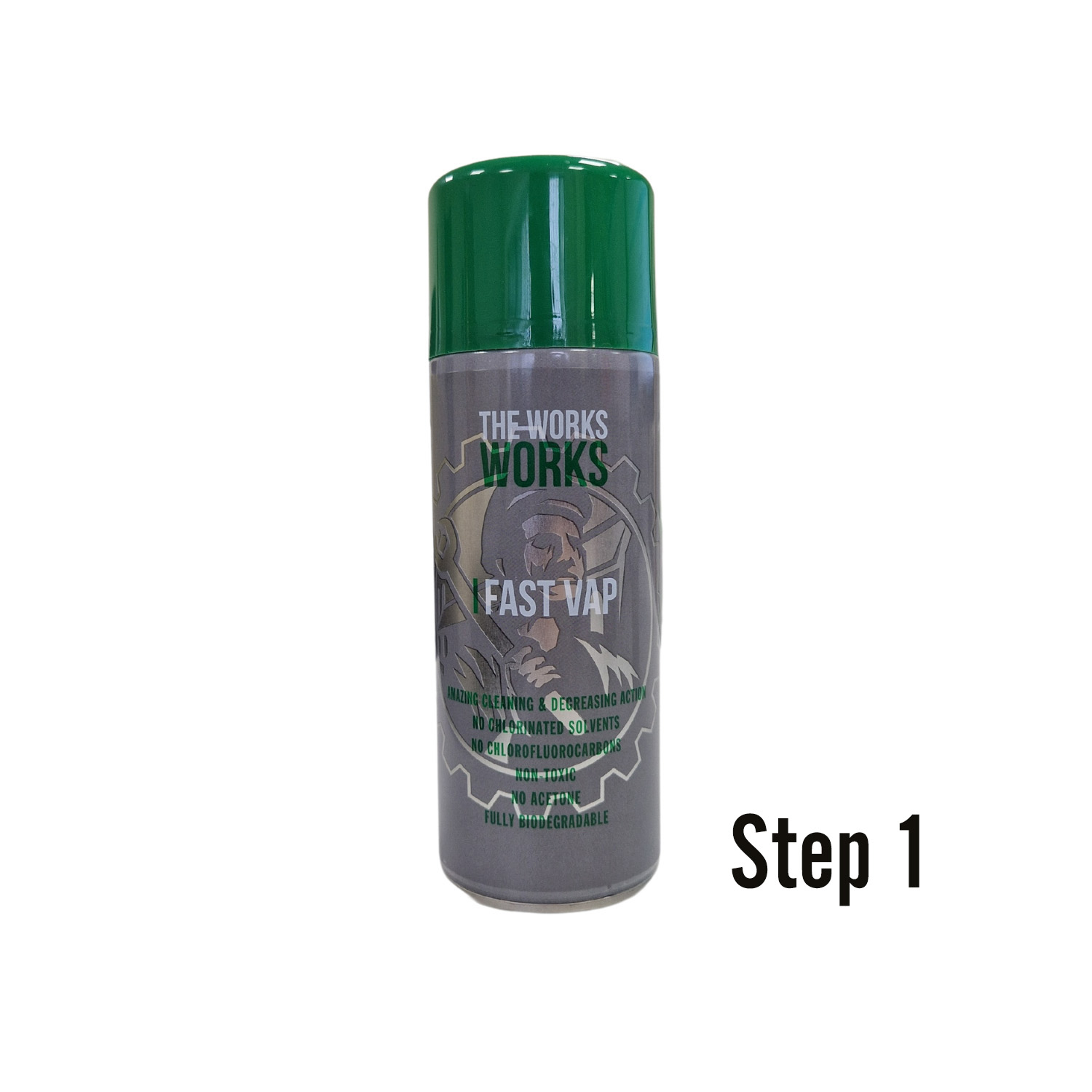
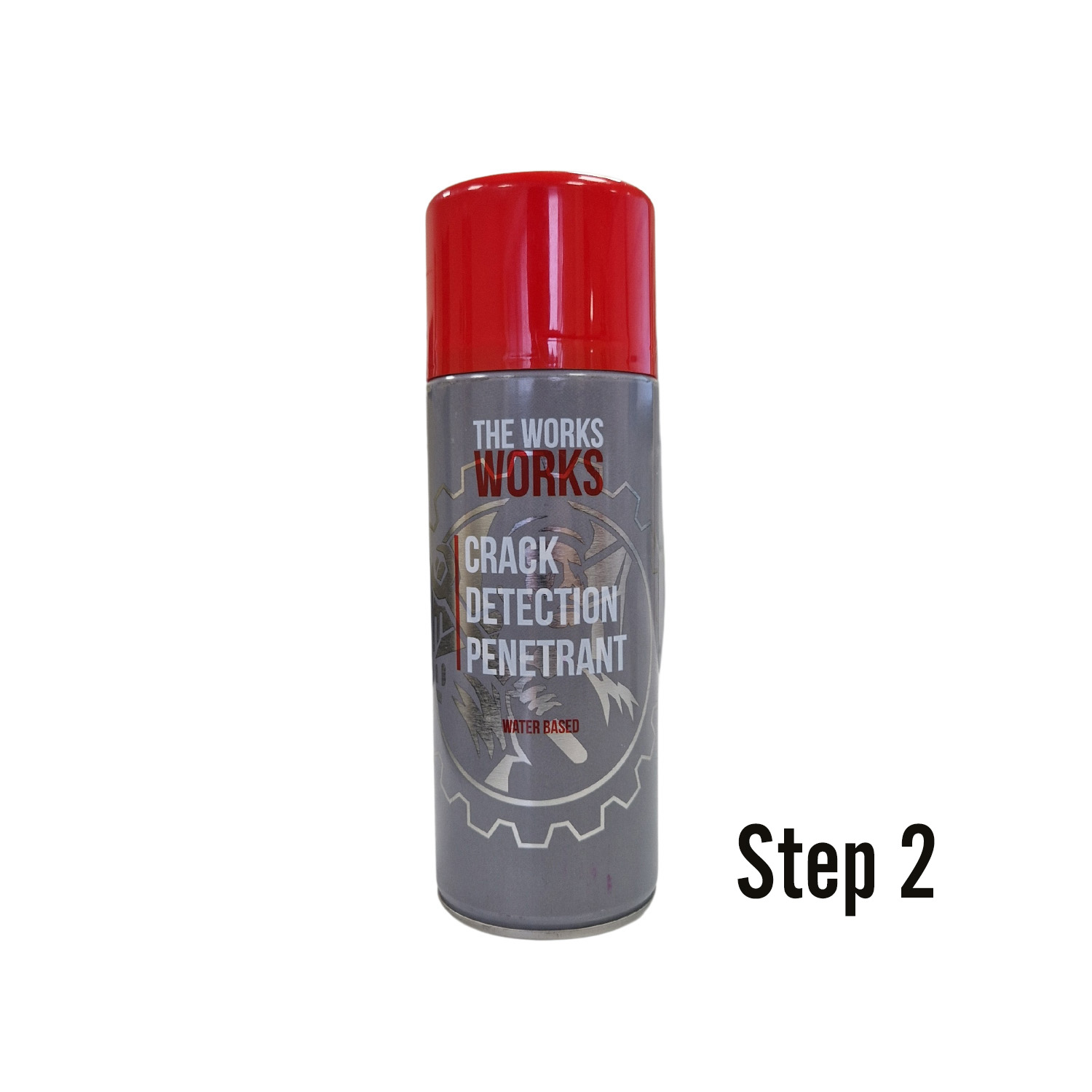
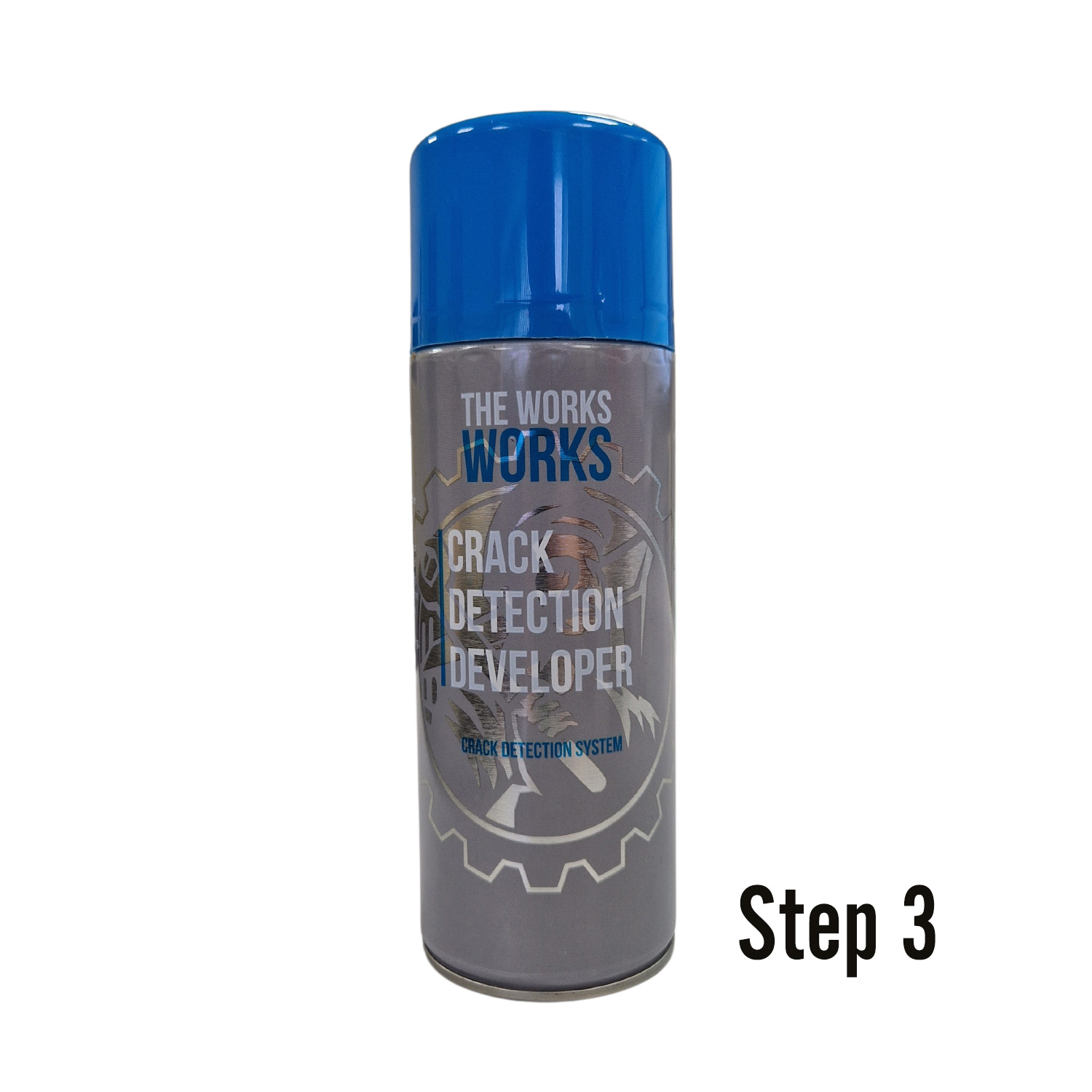
The Works NDT Non Destructive Testing Crack Detection System
Product Overview
-
The Works Non-Destructive Testing NDT crack detection fluids are used to detect casting, forging and welding surface defects, such as hairline cracks, surface porosity, leaks in new products, and fatigue cracks on in-service components.
Read more
Step 1 – Pre-Cleaning:
The Works Fast Vap Cleaner is a fast-evaporating safe solvent with amazing cleaning and degreasing properties. The test surface is cleaned with The Works Fast Vap to remove any dirt, paint, oil, grease or any loose scale that could either keep penetrant out of a defect, or cause irrelevant or false indications. The end goal of this step is a clean surface where any defects present are open to the surface, dry, and free of contamination. The Works Fast Vap is a safe solvent with no chlorinated solvents, no CFC chlorofluorocarbons, non-toxic, no acetones and is fully biodegradeable.
Step 2 – Application of Penetrant:
The Works Crack Detection Dye Penetrant offers excellent creeping properties, vivid violet and is water rinsable. The water-based Crack Detection Penetrant is applied to the surface of the item being tested and allowed "dwell time" between 5 to 30 minutes, to soak into any flaws – smaller flaws require a longer penetration time due to their incompatible nature. It is essential that any excess penetrant will need to be removed from the surface, before the developer is applied, as it may leave a background in the developed area that can mask indications or defects. In addition, this may also produce false indications severely hindering your ability to do a proper inspection.
Step 3 – Application of Developer:
The Works Crack Detection Developer is fast acting giving very clear indications of the presence of flaws. After excess penetrant has been removed, the Crack Detection Developer is applied to the surface of the item being tested. The developer should form a semi-transparent and even coating on the surface. The developer draws penetrant from defects out onto the surface, to form a visible indication, commonly known as bleed-out. Any areas that bleed-out can indicate the location, orientation and possible types of defects on the surface. Inspection of the test surface should take place after 10 to 30 minutes development time. This time delay allows the blotting action to occur.