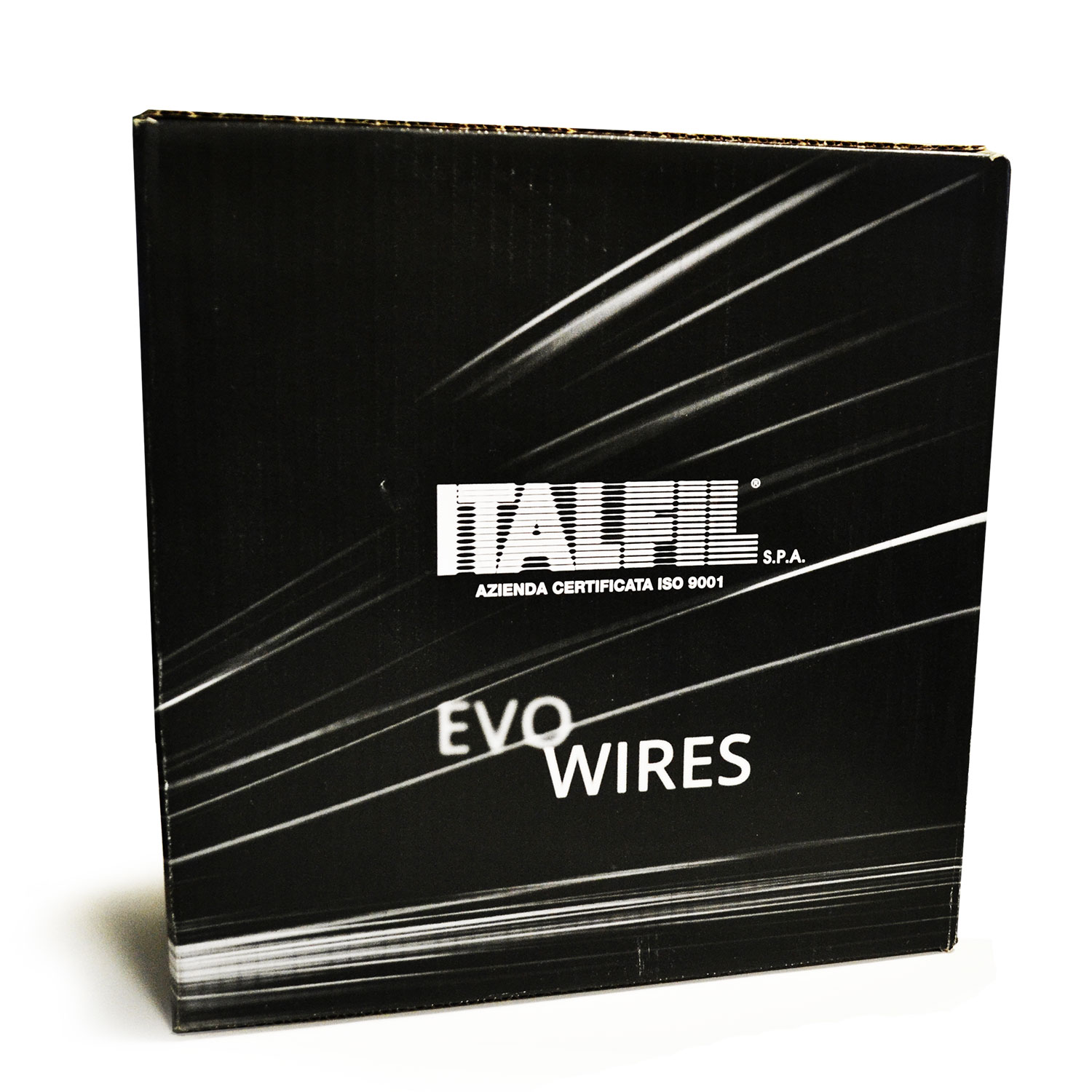
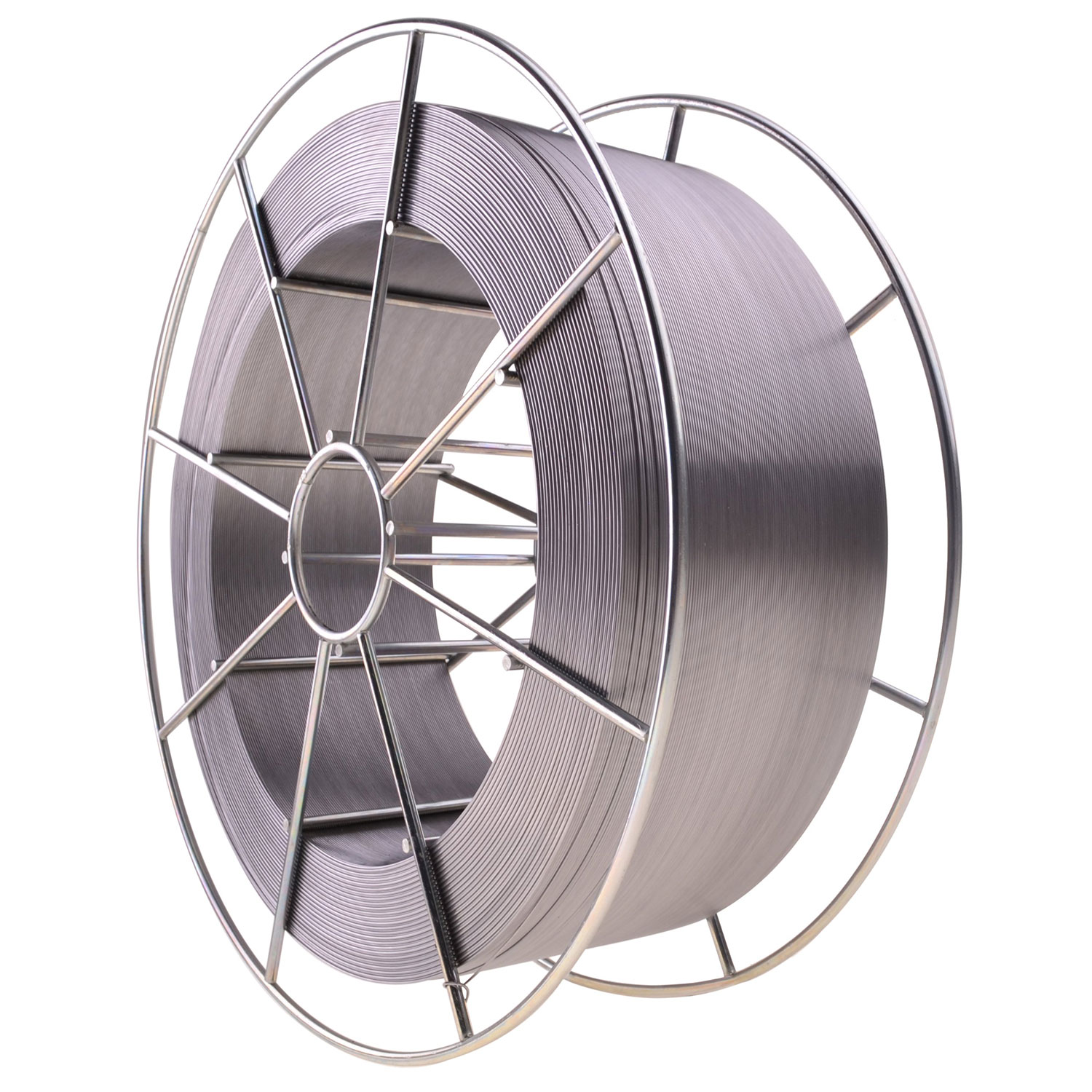
Italfil EVO 2 Premium Un-Coppered SG2 MIG Wire
Product Overview
-
EVO wires are the result of a deep study, research, testing and investment in new production processes and treatments such as dry drawing, in conjunction with the selection of quality raw materials. Every step has been carefully studied in depth in order to ensure the best results, right up to the finished product and packaging. The name EVO is derived from the word Evolution, this un-coppered welding wire is a true evolution in MIG/MAG wire production. When compared to the solid welding wires traditional used during the MIG/MAG welding process on carbon steels. EVO welding wires surpass the characteristics of the copper coated wires with exceptional conductivity, ease of feeding, oxidation protection, whilst eliminating the negative aspects of the traditional wires.
Read more
The benefits of the EVO wires are superior welding performance, increased efficiency which help to reduce overall welding costs. With the absence of a copper coating the EVO wires offer substantially less risk of poor feed ability often caused by clogging in the MIG torch liners from copper flakes, this results in less maintenance downtime and a higher welding duty cycles. In addition to the increased production from higher working duty cycles, the reduction in spatter and silicates during the welding process helps reduce the time and cost of post-weld grinding.
EVO wires also offer an environmental advantage, these also wires greatly reduced the amount welding fume and copper in the welding fume and contributes to a healthier environment in and around the welding workplace. The Low fume emission gives a cleaner working environment within the welders working zone. Increasingly health authorities in many countries are advocating the use of copper-free wires whenever possible to improve the safety of the workplace environment.
Features:
During Tests carried out at the Italian Institute of Welding two wires with same diameter and from the same heat/lot number were tested. The only difference in the type of surface coating, one was a premium copper coating wire and the other was the EVO un-coppered wire. The tests were carried out in accordance with EN ISO 15011-1, the results showed a reduction in the rate of emission of fumes (FER) from the EVO wire of around 8% The analysis of the fume from the EVO wire also showed a 292% reduction in the emission of copper, reducing the amounts from 0,373 mg to 0,095 mg.
EVO wires ensure a smooth and constant feed creating a stable and uninterrupted arc, this helps to considerable reduce the welders down time from having to readjust the welding machine. EVO wires offer an even bigger feeding advantage when used in applications where long conduits are required, which from time to time may develop bends in them.
In spray transfer the smooth and constant feeding accompanied by the stable and uninterrupted arc, will also help to significantly reduce the amount of the spatter when compared to traditional copper wires.
EVO wires offer a considerable reduction of silicates, this benefit can help to drastically reduced clean up times after welding with very good bead appearance. This is major advantage and can help reduce production times when multi runs are being produced, normally the silicates need to be removed prior to the next run.
Reduction of welding defects which helps to reduce regrinding operations that can often waste time and money.
The arc initiation is immediate allowing the arc to stabilize in a much shorter time, this helps to speed up the tacking process when compared to even the best quality copper coated wires currently available on the market.
Evo wires 1.0mm & 1.2mm are supplied on 18kg reels which helps reduce welder down time changing reels by up to 20%, when compared to traditional 15kg reels. The steel wire baskets can be compacted and disposed of easily reducing the cost of waste management.
Evo wires 0.8mm are supplied on 16Kg steel wire baskets.
C E Marking according to EN 13479
Base Materials;
EN 10025 S185, S235, S275, S355, S420, S275M, S275ML, S355M, S355ML, S420M, S420ML
ASTM A131 Grade A, B, D, AH32 to DH36
EN 10208 L210, L240, L290, L360, L240NB, L290NB, L360NB, L360QB, L240MB, L290MB, L360MB, L415MB
API 5LX X42, X46, X52, X60
EN 10216 P235T1, P235T2, P275T1
EN 10217 P275T2, P355N
EN 10028 P235GH, P265GH, P295GH, P355GH
EN 10025 S275, S355, S420, S275M, S275ML, S355M, S355ML, S420M, S420ML
Approximate Welding Parameters;
ø (mm) 0.8
Amps 90 – 160
Volts 18 – 24
ø (mm) 1.0
Amps 120- 250
Volts 22 – 30
ø (mm) 1.2
Amps 220 – 350
Volts 26 – 34
Classification:
SFA-AWS A5.18 ER70S-6
EN ISO 14341-A- G 46 4 C1/M21 3Si1
CSA W48-14 B-G 49A 3 C1 S6
Mechanical specifications;
RM N/mm² 550
Rs N/mm² 450
A%5d > 24
kV (J)-40°C >= 80
Hardness HB
Hardness HRC
Average chemical composition;
C% 0.07
Mn% 1.45
Si% 0.85
P% <0.020
S% <0.020
Cu % < 0,10
Cr % < 0,15
Ni % < 0,15
Mo % < 0,05
Al % < 0,020
V % < 0,030
Zr+Ti% < 0,15
Shielding gas 100% CO2 or Argon + >15-25% CO2 80%