What to consider when purchasing a MIG Welding Torch
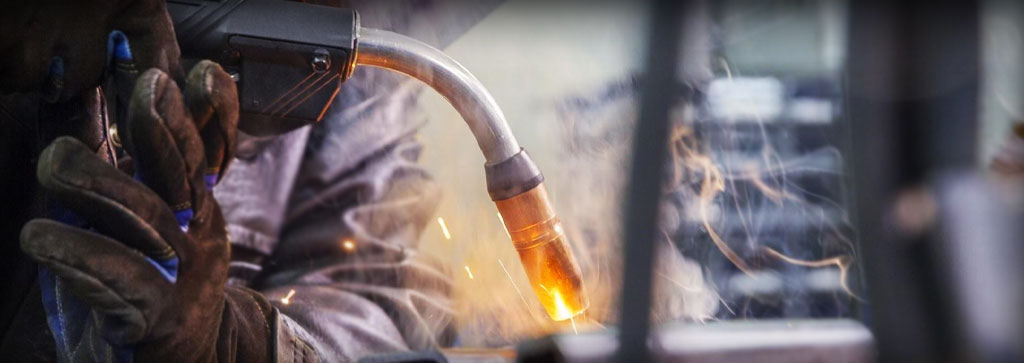
Not all MIG Welding Torches are created equal.
When it comes to purchasing a MIG Welding Torch and the on-going consumables, it can often not be a great deal of thought. However, the wrong choice could have a profound effect on your welding process and could affect the welding equipment’s performance. MIG Welding Torches are the most handled piece of equipment during the MIG welding process and they are exposed to the worst working environments and abuse. This can often have a significant impact on the weld quality, productivity and increase the operator’s downtime. It is often thought that all MIG Welding Torches are the same, so price often becomes a deciding factor when welders considering purchasing a new MIG Welding Torch. In this article ‘What to consider when purchasing a MIG Welding Torch’ we’ll discuss everything you need to think about before buying a MIG welding torch.
Should I compare prices on MIG Welding Torches?
MIG Welding Torches can differ considerably in quality between each manufacturer, the difference can have a profound effect on the performance and total life cost of the MIG torch. Premium quality MIG Welding Torches have been designed to minimise downtime, help eliminate poor weld quality and premature torch failures. All these benefits can deliver significant long-term savings. Normally if the only benefit a MIG Welding Torch has to offer is the low price, it generally means it has been manufactured using low cost components. This means the MIG Welding Torch will not last when compared to higher quality components. Generally low-cost consumables eventually need replacing, these often can be harder to replace and regularly damage secondary parts in the process. Based on the price only and with absence of any other facts to help customers consider, it is understandable that most companies would look at reducing their costs by buying a less expensive product.
Arguably the best MIG Welding Torch on the market?
Bernard Semi-Automatic Air-Cooled Q Type MIG Welding Torches are at the quality end of the market and are manufactured with heavy duty power cables, which have a 60% duty cycle in mixed gases. Built into these heavy-duty power cables are four switch leads, should the two being used get damaged then the other two can be utilised. The Bernard Q MIG Welding Torches are available from 200A to 600A torch. The Q Type MIG Welding Torches are fully industrial-duty and will carry on welding even in the harshest and most arduous working environments.
Features that make a Bernard MIG torch stand out above the rest
The C handle
Bernard Q MIG Welding Torches now come fitted with the new C handle. This handle gives all the benefits of the Bernard T series handle, plus additional ergonomic benefits. The handle has an over mould and cable strain relief, this gives the welder extra comfort at no extra cost. The additional strain relief also helps to protect the power cable by preventing it from kinking and helps to improve the wire feed ability. The triggers on the C handle are designed and built to last and will deliver in excesses of more than one million cycles.
Q T torch neck
The Bernard Q MIG Welding Torches necks are aluminium armoured and are designed to withstand that day to day environments, whilst offering outstanding heat dissipation for longer service life. They are available as either a fixed or rotatable neck. An additional neck grip accessory is also available which is designed to reduce heat exposure for operators who prefer to support the torch by the neck during the welding process.
Quik tip consumables
Bernard consumables are of a much higher quality than most other brands on the market. They are designed to provide a much more stable arc and greater shielding gas coverage of the weld pool to ensure no porosity. We tested Bernard consumables against many other low-cost brands. On site tests have shown Bernard consumables have given three to four times longer contact tip and increased nozzle life. This feature helps to reduce poor weld quality problems caused by inconsistent electrical transfer, which helps eliminate contact tip burn backs, which can be a major source of lost welding hours. The Bernard replacement consumables are designed to eliminate downtime during the welding process, maximise productivity and help reduce operation costs. All these features contribute to a greater return on your investment.
Quik contact tip
Contact tips play a significant role in the MIG welding process, since these are responsible for transferring the welding current across to the wire as it passes through the bore of the tip and the welding arc. Bernard Quik Tips are designed with a threaded taper lock, giving a large contact area between the contact tip and the gas diffuser. This drastically increases tip life by providing reduced resistance, excellent heat transfer, and electrical conductivity. No tools are required, just a quick twist is all it takes to install and remove the Bernard Quik Tip contact tips! The same quality contact tip is used on a 200A to 600A torch and are available for wire diameters from 0.6mm to 3.2mm.
Quik gas diffuses
Bernard Quik Tip gas diffusers have a positive stop which secures the Quik Tip contact tips in a fix position for superior repeatability and consistent quality welds. The position of the contact tip within the nozzle, commonly referred to as the contact tip recess, can also play a crucial factor. The correct contact tip recess position helps to reduce excess spatter, porosity, insufficient penetration, burn-through or distortion when welding on thinner materials. While the ideal contact tip recess position varies according to the application, a general rule of thumb is that as the welding current increases, then the recess should also increase.
The chart below is a guide showing which Quik Tip diffuser should be used.
Recess/
Extension |
Amperage | Wire Stick-Out |
Process | Notes |
1/4” Recess | >200 | 1/2 – 3/4” | Spray, high-current pulse | Metal-corded wire, spray transfer, argon-rich mixed gas |
1/8” Recess | >200 | 1/2 – 3/4” | Spray, high-current pulse | Metal-corded wire, spray transfer, argon-rich mix gas |
Flush | <200 | 1/4 – 1/2” | Short-circuit low-current pulse | Low argon concentrations or 100% CO2 |
Quik Thread system
With the Bernard Quik thread system, removing the nozzles from the diffuser could not be simpler. Just a quick twist is all it takes to remove them for either cleaning or replacing them. They have a heavier wall thickness and insulating material used in the manufacturer of the nozzle. This helps to reduce heat degradation giving the nozzles greater service life. The Bernard Quik Nozzles are available in two orifice diameters for optimal shielding gas coverage – 16mm (5/8”) and 19mm (3/4”).
Quik load liners
Bernard liners are made from high carbon music wire which resists gapping when the liner is bent, helping to eliminate wire feed issues and ensures an exceptionally long service life. Each Bernard liner is 100% tested prior to them being despatched. This ensures it to be the smoothest wire feed in the industry. With the liner retainer being installed inside the torch’s power pin on the first installation, the innovative Bernard ‘Quick Load’ liners eliminate the need to remove the MIG welding torch from the wire feed unit. This saves you from cutting and wasting the welding wire. These liners are installed from the front of the MIG gun by removing the torches front end consumables. Changing a liner can now be achieved in less than half the time required to install conventional liners, increasing production times and reducing labour cost with increased safety. The need to climb up and a change a liner in a semi-automatic MIG Welding Torch connected to a boom-mounted feeder, is now eliminated. The ‘Quick Load’ liner also helps avoid climbing over robotic tooling or transfer systems to remove the torch from the wire feeder. The liner can also be changed from a safe zone in the robotic work cell.
How to change a torch liner in a MIG Welding Torch?
- Remove the front-end consumable (nozzle, contact tip and diffuser).
- Remove the existing ‘Quick Load’ liner from the torch using a set of pliers. Then, remove the protective cap from the new ‘Quick Load’ liner which is going to be fitted.
- Insert the new liner into the torch neck and use the welding wire as a guide. Push the liner down the torch using short strokes to prevent the welding wire and liner from kinking.
- Once the liner has stopped feeding down the torch, give it a final push to ensure it is seated correctly into the liner retainer in the torch’s power pin.
IMPORTANT! Straighten the torch and push the liner back into the gun and hold it firmly in place. Using the liner gauge provided, trim the liner leaving 20mm (3/4”) stick out. Liners trimmed too long or too short can cause serious wire feeding problems. Be sure to always use your liner gauge as instructed to trim the liner to the correct stick out.
- Finally, reinstall the front-end consumables (nozzle, contact tip and diffuser) and you are ready to weld again!